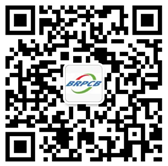
氮化硅(Si₃N₄)基AMB(活性金属钎焊)陶瓷基板凭借其高热导率(>90 W/m·K)、高强度(抗弯强度>800 MPa)以及优异的耐热冲击性,已成为新能源汽车、光伏逆变器等大功率器件的核心封装材料。例如,450/600V车规级IGBT模块多采用DBC陶瓷基板,而800V及更高功率的模块则倾向于使用AMB陶瓷基板。随着SiC功率器件集成度和功率密度的提升,工作热量大幅增加,采用Si₃N₄基AMB陶瓷基板以实现更高的热性能和可靠性已成为行业新趋势。
采用Si₃N₄基AMB陶瓷基板的车规级逆变器
然而,金属化层(通常为铜)与氮化硅基板之间的热膨胀系数(CTE)差异过大,导致热应力问题突出,严重影响了产品的可靠性。本文将从热失配的微观机理出发,解析其影响因素,并提出多维度改善策略,为工程实践提供参考。
从材料组成来看,氮化硅基AMB陶瓷基板由氮化硅(Si₃N₄)、活性钎料层(如Ag-Cu-Ti)和铜(Cu)构成。氮化硅的CTE为3.2×10⁻⁶/K(室温至500℃),而活性钎料层和铜的CTE分别为14-16×10⁻⁶/K和17×10⁻⁶/K。金属化铜层与氮化硅的CTE差异高达5.3倍,温度变化时界面会产生显著的剪切应力。
以基板从25℃升温至200℃(ΔT=175℃)为例,根据双材料梁模型估算,界面剪切应力(τ)可达320 MPa,远超铜的屈服强度(约70 MPa),导致塑性变形与界面损伤。
宏观上,热失配主要表现为以下三种现象:
界面分层:钎料层与Si₃N₄界面因剪切应力剥离。
铜层翘曲:CTE差异导致铜层凸起或凹陷。
裂纹扩展:热循环下,裂纹从界面向基板内部延伸。
Si₃N₄基AMB陶瓷基板结构示意图
热失配问题可从结构、材料和工艺三个方面分析:
结构因素:大面积铜箔与氮化硅陶瓷基板焊接,导致应力集中。
材料因素:铜层厚度增加会放大热失配效应(应力与厚度成正比)。
Ag-Cu-Ti钎料中Ti含量(2-5 wt%)影响界面反应层(TiN/TiSi₂)的厚度与结合强度。
Si₃N₄表面粗糙度(Ra<0.5 μm)与活化处理(如等离子清洗)影响界面结合力。
工艺因素:
典型钎焊温度为850-900℃,保温时间5-10分钟,过高的温度会加剧界面反应层脆化。
快速冷却(>20℃/min)导致残余应力积累,建议采用梯度冷却(先快冷至300℃,再慢冷至室温)。
Si₃N₄基AMB陶瓷基板生产工艺流程图
有限元仿真优化:基于ANSYS等工具优化铜层厚度、陶瓷厚度、图形化布局与过渡层参数,使最大等效应力从320 MPa降至180 MPa。
适用于Si₃N₄基AMB陶瓷基板的热弹塑性有限元模型
低CTE金属替代铜层:采用钼铜(Mo-Cu)复合材料替代铜箔,通过调节钼含量(15-30 wt%)将CTE降至7-9×10⁻⁶/K,更好地匹配氮化硅。
纳米改性钎料:在Ag-Cu-Ti钎料中添加1-3 vol%纳米TiN颗粒,细化界面反应层并提升韧性(断裂能提高30%)。
激光表面织构化:在Si₃N₄表面激光刻蚀微孔阵列,通过机械互锁增强结合强度(剪切强度提升至45 MPa,较纯平面基板提高50%)。
某车规级IGBT模块(1200V/300A)在-40℃~150℃热循环1000次后出现铜层剥离问题。通过采用Mo-Cu(20wt% Mo)复合金属层和激光织构化界面,模块的热循环寿命提升至5000次,界面剪切强度维持在>40 MPa。
石墨烯铜基复合材料:添加0.5 wt%石墨烯可将铜的CTE降至12×10⁻⁶/K,同时保持导电率>90%。
金属-陶瓷共烧技术:借鉴HTCC工艺,实现W/Mo金属与Si₃N₄陶瓷共烧结,避免钎焊界面问题。
结论
通过优化材料选择、改进工艺参数以及采用先进表面处理技术,氮化硅基AMB陶瓷基板的热失配问题得到了有效缓解。未来,随着石墨烯铜基复合材料和金属-陶瓷共烧技术的进一步发展,其在高温、高功率环境下的性能将进一步提升,为大功率器件提供更可靠的解决方案。